Recently, iChEM researcher Xinhe Bao and Xiulian Pan’s group from DICP challenged the traditional Fischer-Tropsch Synthesis (FTS) routes and developed a bifunctional catalyst that synthesis gas (syngas) to light olefins (C2=–C4=) and achieves higher conversion and avoids deactivation. Their research result was published on Science on March 4, 2016, in the title of “Selective conversion of syngas to light olefins” (Science,2016,351,1065-1068). The process has been applied for Chinese invention’s patents and International PCT patents. This achievement has been regarded as a major breakthrough in the field of coal transformation by peers. The Science article also published a review which makes a comment that the catalyst enables the direct conversion of syngas to lower olefins with a surprisingly high selectivity, this process in the industry will be highly competitive in the future.
The Fischer–Tropsch process is a collection of chemical reactions that converts a mixture of carbon monoxide and hydrogen into liquid hydrocarbons. It was first developed by Franz Fischer and Hans Tropsch in Germany, in 1923.Although the process is not perfect, for example, producing large amounts of carbon dioxide, consuming huge quantities of water, poor selectivity and consuming a lot of energy in subsequent process. However, the process has always been considered irreplaceable by International Energy Agency and chemical industry. Now, the researchers from DICP has made a breakthrough, by overcoming the old process with high water consumption and high energy consumption, and directly converting syngas to light olefins with high selectivity. When the conversion rate of CO was 17%, the selectivity of low carbon hydrocarbon products reached 94%, and the selectivity of low carbon olefins (ethylene, propylene and maleic) was greater than 80% which is higher than the maximum limit (58%) of Fischer–Tropsch process.
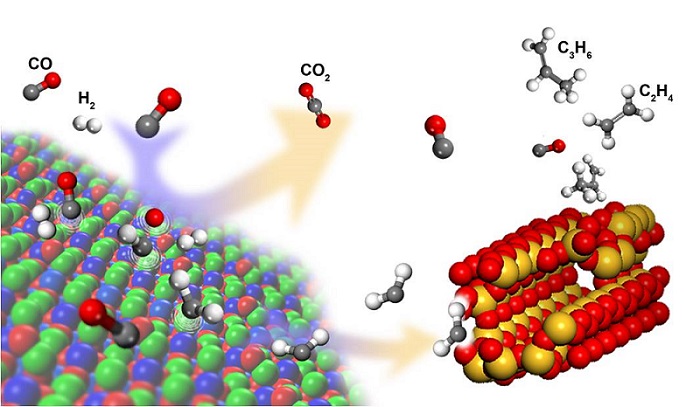
A variety of catalysts can be used for the Fischer–Tropsch process, but the most common are the metals. The CO is activated and then dissociated into C and O atoms on the surface of the metal. The C and O atoms reacted with the hydrogen adsorbed on the surface of the catalyst and formed an intermediate (CH2), followed by the water molecules. The methylene intermediate took part in the reaction through migration, performing free polymerization on the surface of the catalyst, generating hydrocarbon products with different number of carbon atoms (from one to thirty, even hundreds of carbon atoms). The carbon atoms of hydrocarbons are widely distributed, with the low selectivity of the target products. At the same time, this process need to consume a large amount of hydrogen to remove O atom. However, these precious gas were obtained by water gas transform (CO+H2OH2+CO2) with high energy consumption, releasing large amounts of carbon dioxide. The researchers from DICP used a bifunctional catalyst affording two types of active sites with complementary properties. The partially reduced oxide surface (ZnCrOx) activates CO and H2, and C−C coupling is subsequently manipulated within the confined acidic pores of zeolites. CO and H2 are activated over a partially reduced oxide (ZnCrOx) surface, whereas C−C coupling is controlled within the confined environment of zeolite pores with acidic sites. Thus, any measures that could facilitate the transport of intermediates in gas phase should benefit selective formation of olefins. Thus, the CO conversion and selectivity can be tuned at the same time i.e., CO conversion is manipulated via the surface structure of the oxides and the ratio of oxides/zeolite, whereas the olefin selectivity is controlled by the properties of zeolites, particularly the pore structure and acidity.
In the case of without changing the total CO2 emissions, the process used CO instead of H2 to eliminate the redundant oxygen, abandoning the high energy consumption and high water consumption, which successfully answered the concern of Premier Keqiang Li “Less or no water consumption in coal chemical industry”. At the same time, by combining the metal oxide catalysts with zeolite creatively, they realized the effective separation of CO activation and intermediate coupling, to control the growing radicals in a “cage(zeolite)” producing the target products what we want (low carbon olefin).These findings open up a new avenue for development of syngas-to-olefin technologies, which may allow utilization of coal- and biomass-derived syngas with a low H2/CO ratio.
In addition to saving water and reducing CO2 emissions (shorten the process, reduce the energy consumption), there are other high economic benefits. According to the preliminary assessment of the Sinopec Engineering Construction Company Limited (SEI), under the existing conditions, the internal rate of return (IRR) is more than 14%. Many domestic and foreign chemical companies are very much interested in the further application of the process. After careful assessment and consultation, DICP has reached an initial agreement with famous domestic and foreign chemical companies, to cooperate in the preparation of the catalyst and the development of the process, striving to achieve industrial demonstration, industrialization and substantial productivity as soon as possible.
When the German BASF company expert Dr.Schwab ph.d., understood the basic situation of the process and surprisingly asked " Why did't we put forward this idea at first?" , Prof. Xinhe Bao proudly replied that "You had a lot of ideas until, and now it is our turn".The confidence comes from an outstanding research team in support of China increasing scientific research ability. The team cost more than nine years, and cooperated with domestic research institutes including Hefei Synchrotron Radiation Light Source (HLS), using a variety of independently developed research apparatus. During this period, a Chinese patent and an international patent application under the Patent Cooperation Treaty have been declared and is pending.
This work was financially supported by the National Natural Science Foundation of China, the Ministry of Science and Technology of China, the “Strategic Priority Research Program” of the Chinese Academy of Sciences and Dalian Institute of Chemical Physics Fundamental Research Program for Clean Energy.
paper link:http://science.sciencemag.org/content/351/6277/1065.full